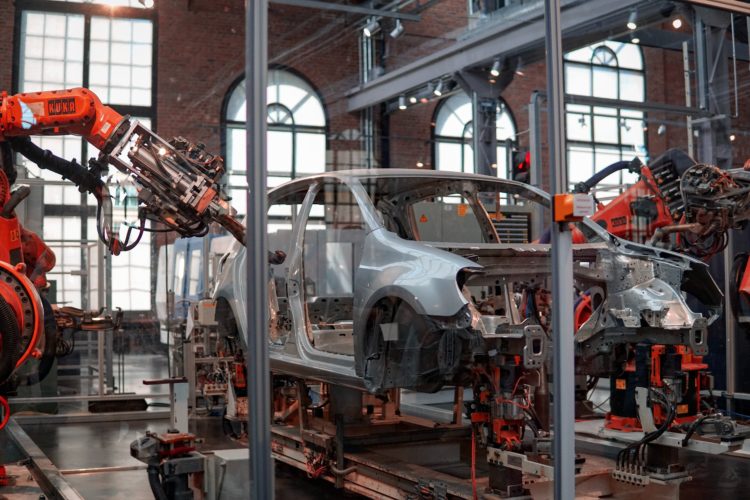
La commande prédictive et ses applications industrielles
Dans son discours d’ouverture, M. Jacques Richalet, le premier apôtre de la commande prédictive en France, a souligné les principaux avantages de la commande prédictive PFC (Predictive Functional Control) : performances supérieures par rapport au PID et facilité d’implémentation et de réglage. Depuis sa première mise en place, en 1968, le champ d’application de la PFC s’élargit constamment, en améliorant les performances des procédés de tous les types d’industrie : la pharmacie, la chimie, la sidérurgie, sans oublier la pétrochimie.
Le premier témoignage de la journée a montré l’efficacité du PFC dans la commande d’une centrale thermique à flamme Alstom. Le département R&D du constructeur a étudié la faisabilité de l’utilisation du PFC pour la régulation de deux boucles réputées difficiles : la tenue du niveau d’eau dans le ‘ballon’ et la tenue des températures de la vapeur surchauffée, qui agissent directement sur le rendement de la centrale. Les résultats obtenus sur le simulateur ont montré que la commande prédictive a permis d’assurer les performances imposées par le cahier des charges.
La présentation suivante a décrit la démarche des services techniques de Sanofi, qui se sont orientés vers la commande prédictive comme solution en termes de régulation de température interne des réacteurs de procédé chimique. L’utilisation du même réacteur pour la synthèse des différents produits a mis en évidence l’intérêt de la commande à base de modèle.
L’ECAM et EDF R&D ont présenté le résultat d’une collaboration, qui leur a permis d’améliorer l’efficacité énergétique des groupes frigorifiques dont EDF dispose sur le site des Renardières. Pour ces types de processus, présentant des fortes perturbations, le régulateur PID est assez délicat à ajuster. Le PFC a remplacé les régulateurs classiques PID afin de réguler la surchauffe en sortie d’évaporateur, la pression de condensation et la puissance frigorifique. Les bonnes performances obtenues ont déterminé l’équipe de recherche à étendre l’approche prédictive sur d’autres types de machines thermiques : chaudière, four à induction…
Tous les intervenants ont souligné les performances nettement meilleures obtenus par la commande prédictive par rapport au PID. La connaissance du comportement du procédé représente un des points forts de la commande prédictive. Ainsi, le modèle dynamique, utilisé pour prédire le comportement du système est le constituant de base de cette méthode. Les solutions présentées lors de cette demi-journée d’études ont été réalisées en assimilant les procédés à commander à des systèmes de premier ordre avec retard pur. Dans ce cas, la mise en œuvre de la commande PFC ne nécessite que trois paramètres à identifier : un gain statique, une constante de temps et un retard pur. Pour des processus plus complexes dont les non-linéarités ne peuvent plus être négligées, l’identification d’un modèle de commande peut s’avérer une tâche plus difficile que la conception de la loi de commande.
Pour répondre à cette problématique, Acsystème et le Lagep (Laboratoire d’automatique et des génies des procédés) ont initié une thèse Cifre portant sur l’identification paramétrique en boucle fermée par une commande optimale.
Et pour aller plus loin, un article d’Usine Nouvelle sur « l’automatisme en mode lean »
Petru-Daniel Moroşan, ingénieur et docteur en automatique