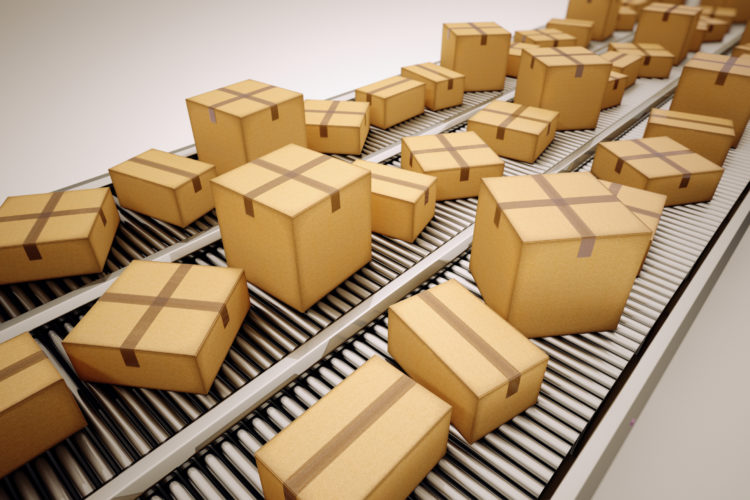
Automated, optimised palettisation: new solutions!
Task automation saves valuable time in manufacturing, inventory management and package preparation. Palletisation is one of the regular steps in an industrial logistics flow. In most cases, products are homogeneous, and the traditional robot palletising solutions are sufficient. When packages vary in size, shape, and weight, stacking them in a stable, efficient, and optimal way can be a challenge.
How should units of various sizes be stacked efficiently and harmoniously in a fully automated way? Combinatorial algorithms can quickly generate an optimised compact palletising plan.
Such algorithms can either be embedded into palletising robots or can be used to facilitate the work of operators, by providing them with a pre-built palletising plan. In all cases, they are a time-saving solution whilst improving the efficiency, health, and safety of operators.
Two possible configurations
In the first case, the packages come one after the other (“with the stream”) and must be placed on the pallet in the best possible way, without knowing in advance what comes next. This is the so-called “inline” palletising method that is generally found on logistics platforms.
In the case of order picking, all the items to be palletised are known in advance. This situation, known as “offline”, is less constrained by the execution time. Exhaustive knowledge of the items to be palletised makes it possible to use powerful combinatorial algorithms.
Order picking
Acsystème has developed palletising solutions for order picking. Some of these are especially efficient for a large number of packages of each product reference (several dozen packages per reference). By considering the specific characteristics of this type of order, Acsystème has designed combinatorial algorithms which make it possible to generate a compact palletisation plan quickly.
The 3 stacks below represent the palletisation calculated in 3.4 seconds for a dataset of 7 items present at least 50 times each.
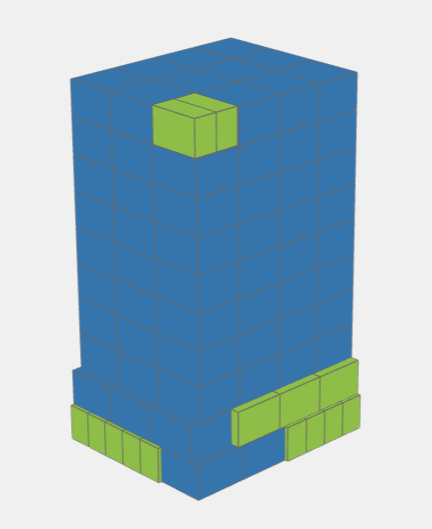
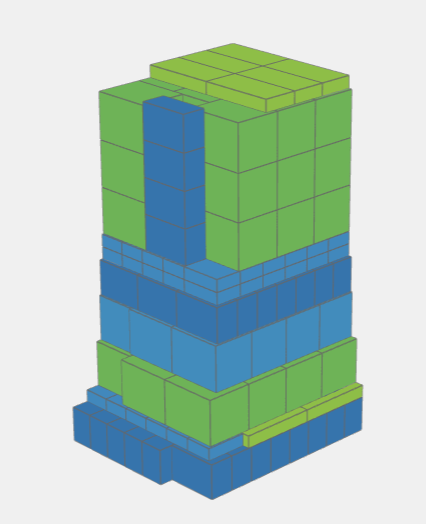
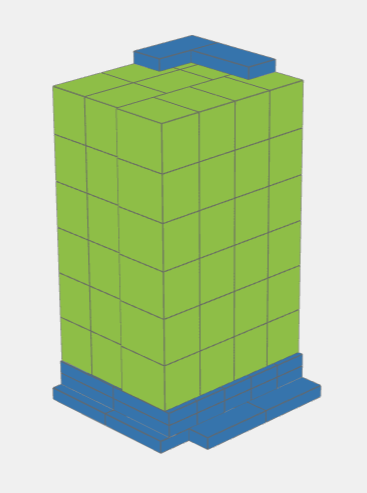
The 3 stacks below represent the palletisation calculated in 3.4 seconds for a dataset of 7 items present at least 50 times each.
As is the case for other solutions, the algorithm can calculate the number and size of pallets required from creation of the order. As a result of optimisation of parcel placement, the algorithm reduces the number of pallets needed compared to manual palletising.
The algorithms previously developed by Acsystème dealt with the requirements for palletising parcels or planks. Geometric optimisation extends the scope of problem resolution:
- Loading of trucks, with the possibility of considering additional criteria such as transit routes or delivery circuits,
- Loading of containers, with or without preloading, addition of unitary elements, optimisation of weight distribution, etc.
Going further with artificial intelligence
Each optimisation topic is specific. A preliminary analysis of the specifications and its underlying needs is therefore an important step in the project. It makes it possible to develop the most relevant methods to meet the constraints, amongst the new artificial intelligence technologies.